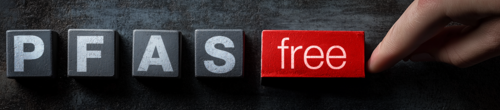
Per- and polyfluoroalkyl substances (PFAS), also usually called “forever chemicals”, have attracted significant regulatory attention worldwide due to their indelible nature, potential health risks, and environmental impact. These synthetic chemicals, used in numerous industrial and consumer products from non-stick cookware to medical devices, mechanical seals as well as applications where functional surfaces with non-sticking and low friction properties required. PFAS polymers do not break down easily, leading to bioaccumulation in both wildlife and humans. Industries are actively seeking viable PFAS alternatives to mitigate these challenges and comply with evolving global regulations, including the European Union's progressive restrictions under REACH, the United States' state-led standards alongside emerging federal guidelines, and coordinated international efforts led by organizations like UNEP to limit PFAS usage and contamination.
PFAS Regulations |
|
European Union (REACH) | Learn more |
United States (EPA) | Learn more |
United Nations Environment Programme (UNEP) | Learn more |
Tightening PFAS regulations are pushing industries to re-evaluate processes and invest in greener alternatives. Companies across sectors - such as food packaging, electronics, energy, aerospace, and automotive - are exploring PFAS-free materials and remediation methods in response to growing legislative pressure and public concern.
A key part of this shift involves strengthening supply chain controls, with updated supplier contracts and material specifications that demand PFAS disclosure and restriction. Internal policies increasingly require action plans when PFAS are identified. For example, leading manufacturers in both the automotive and electronics sectors are phasing out PFAS and committing to safer substitutes. While these efforts signal real progress, the transition is not without challenges - especially when evaluating the limitations of current alternatives.
Replacing PFAS in industrial applications poses major challenges. PFAS alternatives often fall short in key areas like lubrication, durability, and chemical resistance. They struggle to match PFAS’s ultra-low friction and non-stick properties, which can lead to higher wear, increased friction, and more frequent maintenance. Most replacements degrade more quickly under high heat or harsh chemicals, reducing surface lifespan and driving up costs and downtime. Some require hazardous solvents, raising additional health and safety concerns. Since many manufacturing processes are optimized for PFAS, switching often demands costly adjustments.
While promising substitutes exist, many are not yet scalable or fully developed. Developing PFAS-free solutions with comparable performance involves high R&D and requalification costs. A lack of long-term field data further delays adoption, as industries remain cautious about the reliability and durability of newer materials.
Thin film technologies offer a promising alternative to PFAS-based coatings and lubricants for many industrial applications. These advanced PFAS-free coatings can provide similar or superior properties while reducing environmental and regulatory concerns. They offer high durability, extend the lifespan of functional surfaces, and reduce maintenance needs. In many cases, they protect against oxidation, chemical attack, and mechanical wear, making them ideal for harsh environments.
For instance, Oerlikon’s advanced Diamond-Like Carbon (DLC) coatings like BALINIT® MILUBIA and ceramic coatings like BALINIT® CNI can replicate the low-friction behavior of PFAS, improving non-stick properties and reducing abrasive wear even under challenging conditions. One of the key advantages of advanced DLC coatings is their combination of a low friction coefficient (typically 0.1-0.2 against steel counterparts) and high hardness (up to 45 GPa for BALINIT® MILUBIA), making them an environmentally friendly alternative to PFAS solutions. Additionally, for applications requiring both good corrosion resistance and anti-stick properties, BALINIT® CNI can be an effective solution.
Furthermore, thin film coatings do not contain harmful fluorinated compounds, ensuring compliance with global PFAS bans (e.g., EU REACH, EPA regulations) and offer a sustainable PFAS alternative with minimal environmental impact. Many thin film deposition techniques (e.g., PVD, CVD) can be integrated into existing production lines, adjusting hardness, friction, thickness, and adhesion based on specific application needs.
In summary, thin film technologies provide a viable, high-performance alternative to PFAS-based coatings, offering superior wear resistance, friction reduction, and environmental compliance. Their durability, chemical stability, and suitability for high-temperature applications make them an ideal choice for industries looking to transition away from PFAS while maintaining performance and efficiency. Contact us to discuss in detail how we can help you to transition away from PFAS today.
© Copyright 2025 OC Oerlikon Management AG
Back to top keyboard_arrow_up