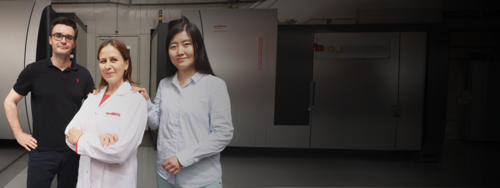
Everyday R&D, Uncommon Results
Oerlikon’s investments in R&D drive our continued commercialization of groundbreaking products and solutions for customers in the automotive, textile, polymer processing, tooling, space and aviation sectors.
Join our R&D team