Aerospace components must withstand the most demanding conditions and comply with strict safety and environmental regulations. Oerlikon Balzers coatings are designed to meet these challenges - during the production of components and tools and throughout their service life.
Actuation systems
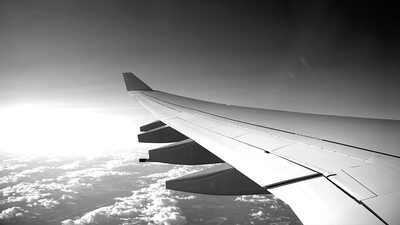
Reduction of the danger of seizure of flight control systems thereby increasing operational safety significantly.
Actuation systemsCompressors
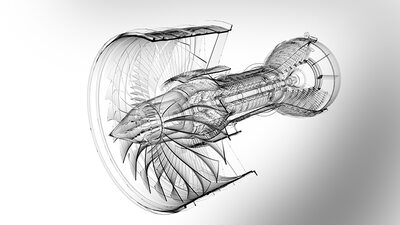
- Abradable coatings for clearance control boost engine efficiency
- PVD coatings protect compressor blades against erosion
Landing gears
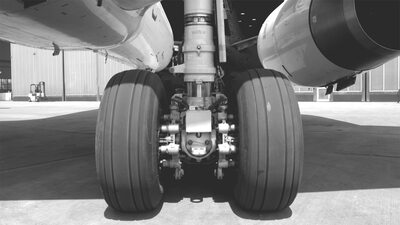
Hard face coatings deliver durable resistance against fretting, sliding, general surface wear and corrosion. They provide an excellent choice to replace hard chrome plating.
Landing gearsInterior decoration
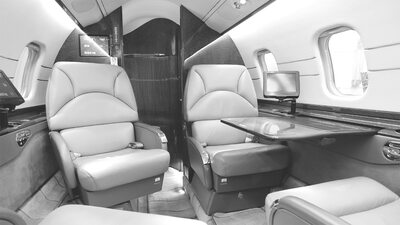
Black and grey colored coatings make instrument dials non reflective.
Aircraft interior designTools for chassis processing
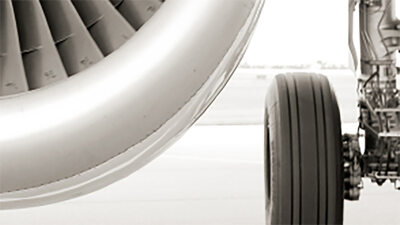
Requirements:
- High thermal load
- High specific cutting force
- Strong abrasive wear by fiber reinforcement
- High stick on inclination
Hydraulic systems, Fuel pumps, Air management systems
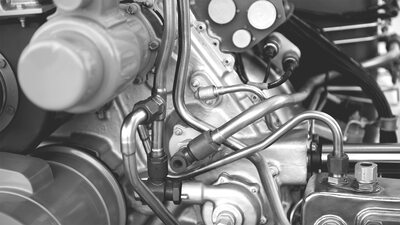
Our coatings reduce friction and protect against wear to increase component service life.
Hydraulic systemsEngine pylons
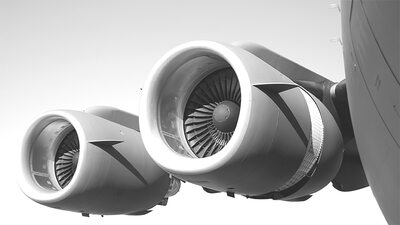
Coatings reduce the danger of fretting wear and corrosion of the engine / wing attachment system which improves overall reliability.
Engine pylonsTools for engine processing
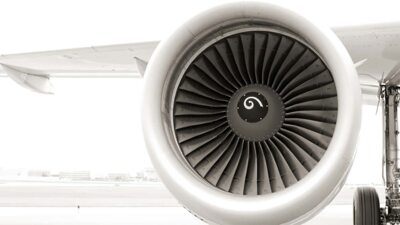
Requirements:
- High thermal load
- High specific cutting force
- Strong abrasive wear by high Cr- and Ni-shares
Tools for structure development
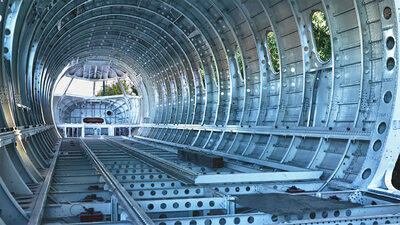
Requirements:
- High thermal load
- High specific cutting force
- Strong abrasive wear by fiber reinforcement
- High stick on inclination
Oerlikon Balzers now has Nadcap accreditation in Guelph, serving the US and Canadian aerospace markets. For a full listing of our other certified centres, please click here.
Take off more easily with BALINIT
The aerospace industry is marked by ever shorter development and manufacturing cycles, enormous quality and safety demands and increasing environmental protection requirements. BALINIT® coatings make a significant contribution to mastering all these demands.
Tribological wear, friction and mechanical impacts take their toll on components, which, during their service life, must withstand wear, corrosion and high loads, whilst being lightweight and exhibiting low-friction. The production of innovative and cost-effective aerospace components is also hugely challenging: cutting tools must resist wear under severe operating conditions, ranging from high cutting temperatures to heavy loads causing friction and problematic chip removal.
BALINIT® coatings fulfil all these requirements – and are based on an environmentally-friendly, future-oriented coating technology. Long approved in the aerospace industry and applied in many domains, these thin PVD coatings exhibit high hardness and decisively reduce friction and wear. Depending on the application, surface treatment improves the service life, productivity and quality of tools and components.