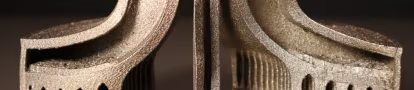
Laser-Based Powder Bed Fusion of Metals (PBF-LB/M) has revolutionized metal additive manufacturing, enabling the production of intricate, high-performance components that were once impossible with traditional methods. By selectively melting fine metal powders layer by layer, this technology provides exceptional design freedom and material efficiency, making it a cornerstone of industries like aerospace, medical, and automotive manufacturing.
However, despite its advantages, PBF-LB/M faces key challenges that hinder widespread adoption—particularly in terms of productivity and sustainability. The process can be time-intensive due to limited build rates, often constrained by laser power and scanning strategies. Additionally, material waste, energy consumption, and emissions from the melting process need to be considered for the assessment of the environmental impact.
InShaPe was an EU-funded project with a total budget of over 7.2 million € spread over 11 partners across Europe and additionally Israel. Together the consortium combined expertise in PBF-LB/M, laser processing, material science, temperature sensing and Artificial Intelligence. More information can be found at the official InShaPe Homepage.
InShaPe addressed the aforementioned drawbacks through innovations in laser beam shaping and process optimization, which is crucial for enhancing efficiency and ensuring a more sustainable future for additive manufacturing. The KPIs to be reached in the project were:
as compared to current best-in-class PBF-LB/M.
Within the InShaPe project, Oerlikon presents the impeller as a key use-case for laser beam shaping in PBF-LB/M. Impellers play a vital role in pumps and compressors used in various industries, including industrial compressors, oil and gas, and aerospace. Closed impellers offer enhanced efficiency, structural integrity, and improved performance with volatile liquids.
Manufacturing these impellers poses challenges. Traditional casting methods risk internal defects and limited surface quality, while machining requires separate parts to be welded, increasing costs and complexity. To overcome these limitations, Oerlikon focuses on PBF-LB/M to produce closed impellers in a single piece, eliminating assembly issues while enabling the fabrication of complex internal geometries.
For high-performance aerospace components, IN718 is the material of choice due to its exceptional strength at high temperatures and superior corrosion resistance. These properties make it ideal for demanding environments where durability and reliability are crucial. For the InShaPe project, both the research and the impeller printing were carried out using Oerlikon’s MetcoAdd™ 718C – a premium, gas-atomized IN718 powder specifically developed for additive manufacturing. With its excellent flowability, controlled chemistry, and consistent particle size distribution, MetcoAdd™ 718C ensures the process stability and material performance required for aerospace and other high-end applications.
Figure 1: Render of the use-case of Oerlikon: An impeller for space applications.
Oerlikon’s main objective was to achieve a build rate of 40 cm³/h, with the State-of-the-Art (SotA) achieving 15.1 cm³/h today, while ensuring a relative density of over 99.8 %. To tackle this, various ring-shaped laser irradiation profiles were investigated, ranging from outer diameters of 350 µm to 550 µm and having different ring thicknesses. The laser power was ranging from 700 W – 1300 W, the scan speed from 400 mm/s – 3000 mm/s and the hatch distance from 0.1 mm – 0.4 mm. In total, over 500 specimens were investigated and their relative density was evaluated using the Archimedean principle.
The best results were achieved using a ring-shaped laser irradiation profile with an outer diameter of 350 µm and a ring thickness of 120 µm, subsequently called Ring-350-120. The chosen parameters result in a theoretical build rate of 93.3 cm³/h, while ensuring a relative density of > 99.8 %. With this parameter, a section of the impeller was printed alongside test specimens to ensure the buildability of the full impeller, as shown in Figure 2.
Figure 2: Printed impeller section (bottom left) and cross section along build direction of test specimen (bottom right). The relative density based on image analysis is 99.81 %. On the top the used ring-shaped laser irradiation profile Ring-350-120 is shown alongside the State-of-the-Art Gaussian beam with a spot size of 80 µm (Gauss-080).
To assess whether InShaPe’s KPIs could be reached, two identical impeller including support structures have been printed with the parameters developed through InShaPe, using the Ring-350-120, and using SotA parameters utilizing a Gaussian beam with a spot size of 80 µm. An image of both printed impellers is shown in Figure 3.
Figure 3: Images of the full impellers to assess InShaPe’s KPIs. Left: Impeller printed using the parameters developed through InShaPe and using the Ring-350-120. Right: Impeller printed using the SotA parameters and a Gaussian beam with a spot size of 80 µm.
Electrical power monitoring was performed during the build jobs to assess energy consumption using an A. Eberle PQBox 150. This device records voltage and current and automatically calculates power consumption, offering precise insights into the machine’s energy usage throughout the process. Scrap generation was quantified by tracking the mass of powder and parts at key stages of the build process. The following mass values were recorded:
The cost was calculated using standard accounting practices within Oerlikon, which considers the pre- and post-processing of the print as well as the printing process itself, the impeller with the SotA parameters. The results are shown in Figure 4:
The InShaPe project has achieved remarkable advancements in metal additive manufacturing, significantly improving both productivity and sustainability, therefore providing a greener, more efficient future for metal additive manufacturing!
By increasing the nominal build rate by a factor of more than six, the printing time for the Oerlikon impeller was reduced by 65 %, bringing the process closer to the project's target of a sevenfold increase.
Despite utilizing a laser power of 1300 W, the overall energy consumption decreased by 58 %, nearly meeting the targeted 60 % reduction. This efficiency gain is primarily attributed to the significantly shorter build time. Additionally, waste reduction proved to be a major success, with scrap generation lowered by 73 %. The condensate, mainly generated through material evaporation, is the biggest contributor to these reductions. The sieving residue, a key indicator of spatter formation, was reduced by 37 %.
Given that printing time is the dominant cost factor, the increase in productivity led to a 57% reduction in production costs, exceeding the project's 50% target.
At Oerlikon, we are proud to have contributed to the InShaPe project, demonstrating the transformative potential of laser beam shaping for metal additive manufacturing. The results speak for themselves – significant improvements in productivity, cost-efficiency, and sustainability.
By leveraging beam shaping in PBF-LB/M, we achieved a sixfold increase in build rate, while reducing energy consumption, scrap generation, and overall production costs. These advancements not only benefit aerospace applications but also pave the way for broader adoption, beyond high performance applications, that demand precision, reliability, and environmental responsibility.
This breakthrough reinforces Oerlikon’s commitment to driving innovation in advanced manufacturing, helping industries push technological boundaries while prioritizing efficiency and sustainability. With InShaPe, we have set a new standard, proving that greener, more efficient metal 3D printing is not just a vision – it’s a reality.
The work doesn’t stop here. We will continue refining and expanding these technologies, ensuring that laser-based powder bed fusion remains a game-changer for advanced manufacturing.
As we move forward, Oerlikon remains committed to turning innovation into impact. Through our comprehensive additive manufacturing solutions, from advanced metal powders to high-quality print services, we support customers across industries in bringing reliable, efficient, and sustainable products to market. Whether you're looking for certified materials, application engineering, or series manufacturing, Oerlikon is your trusted partner in additive manufacturing.
Let’s shape what’s next – together.
© Copyright 2025 OC Oerlikon Management AG
Back to top keyboard_arrow_up