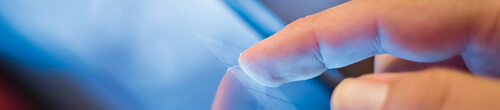
Choose your country / language
Skiving on the Rise: The Third Generation of the PVD Coating Significantly Extends Tool Service Life
The demands on gear quality are continuously growing – especially for gears used in electric vehicles. As a result, skiving is increasingly being preferred over traditional machining techniques, as it produces significantly superior surface finishes and offers greater flexibility for corrections during manufacturing. BALINIT® ALCRONA EVO from Oerlikon Balzers is a high-performance coating that has been specifically developed to further optimize the service life of these expensive tools and reduce production costs in the long term.
Gears are fundamental to mechanical engineering: without them, no machine or device would function, from medical instruments and watches to domestic gas meters and large-scale mining equipment. Their sizes vary accordingly, ranging from less than a millimeter to several meters in diameter. A substantial proportion of the world’s gear production is intended for vehicles – cars, trucks and tractors. Gear teeth are manufactured using high-precision techniques including hobbing, power skiving, broaching and shaping, and across the board the expectations when it comes to quality and precision are rising.
Since machine hour rates are the most significant cost factor for manufacturers, their goal must be to reduce machining time per part while increasing tool service life. The longer a tool can operate without compromising on quality, the less machine downtime there will be, resulting in a more economical production process. The key question is how to minimize tool wear, especially crater and flank wear.
BALINIT ALCRONA EVO excels in skiving applications. Image: © Liebherr / Oerlikon Balzers
BALINIT ALCRONA EVO excels in skiving applications. Image: © Liebherr / Oerlikon Balzers
BALINIT ALCRONA EVO: 30% Less Wear for a German Automotive Manufacturer
Oerlikon Balzers has taken the proven universal coating BALINIT ALCRONA, introduced in 2004, and enhanced it to create BALINIT ALCRONA EVO. In terms of performance and efficiency, it even surpasses its high-performance predecessor, BALINIT ALCRONA PRO, increasing tool service life by more than 30%.
The reasons for this improvement in performance are the coating’s specific advantages:
BALINIT ALCRONA EVO therefore enables higher cutting speeds and shorter production times per part. The cost per part, based on machine hour rates, decreases – and productivity increases.
A German automotive manufacturer saved half a million euros a year by switching from BALINIT ALCRONA PRO to BALINIT ALCRONA EVO. Tool service life was extended by 30%, eliminating the need for 300 new tools – a clear benefit both financially and environmentally in terms of resource consumption.
A Win-Win for Small-Batch Production
Thanks to the wear-reducing properties of BALINIT ALCRONA EVO, less material needs to be removed during regrinding. This is a particular advantage in small-batch production, as it significantly increases the number of possible regrinding cycles – resulting in considerable annual savings given the relatively high cost of new tools.
One gear manufacturer reported a 34% increase in service life of HSS skiving cutters coated with BALINIT ALCRONA EVO during dry machining, along with a 50% decrease in flank wear. As a result, the regrind volume decreased while the number of regrinding cycles increased – reducing tool costs per part by 25%.
Skiving – A Rising Trend in Gear Manufacturing
While not entirely new as a technology, skiving is currently one of the most prominent trends in gear production. As the use of shaping and broaching declines, skiving stands out due to its versatility and performance: it delivers more precise results, allows relatively high cutting speeds, and provides more options for in-process corrections than shaping or broaching.
Skiving Also Booming Thanks to E-Mobility
Skiving is often used for planetary gears, so it is also gaining traction as demand continues to grow for electric vehicles. Skiving is faster than shaping, offers significantly better surface finishes, and allows more flexibility for adjustments during production.
Manufacturers face another challenge: electric vehicles require larger and broader gears to handle high torque from a standstill. These gears must also be machined with greater precision to eliminate noise, which is less critical in combustion engines due to the sound from the engine.
A gear manufacturer confirmed a 34% increase in service life for HSS skiving cutters coated with BALINIT ALCRONA EVO under dry machining conditions. © Liebherr / Oerlikon Balzers
The Critical Factor: Correct Edge Preparation for the Respective Application
Gear machining – and particularly skiving – requires extremely sharp tools. Moreover, this process creates fine chips, and there is a risk of the cutting edge breaking when machining high-strength materials. That means correct edge preparation and pre-treatment of the tool are essential.
Oerlikon Balzers has extensive technological expertise in the gear manufacturing sector and can offer customers a unique combination of tool pre-treatment, coating and post-treatment services.
Requirements vary by application, and factors such as the material being machined and the cutting parameters must be considered – only then can tools be optimized for their intended use. For example, skiving requires cutting edge preparations between 7 and 10 µm, whereas shaping needs a more robust edge with a higher coating thickness. Close collaboration with the customer and the grinding specialist is therefore indispensable, and will become even more important as requirements for precision and efficiency continue to increase.
Broaching and hobbing tools coated with BALINIT ALCRONA EVO. © Oerlikon Balzers