In 2022, our operations, consisting of 166 operational sites, consumed a total of 428.8 GWh of energy. This represents an increase of 4.9% compared to 408.6 GWh in the 2019 baseline year, due to the additional sites from acquisitions.
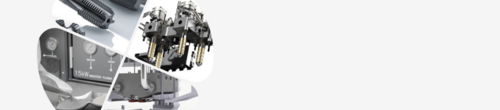
GRI 302-1,3,4; GRI 3-3; SASB RT-IG-130a.1
In 2022, our operations, consisting of 166 operational sites, consumed a total of 428.8 GWh of energy. This represents an increase of 4.9% compared to 408.6 GWh in the 2019 baseline year, due to the additional sites from acquisitions.
Compared to 2021, excluding acquisitions, we reduced energy consumption in our operations in 2022 by 2% (2021: 410 GWh). In 2022, the percentage of energy Oerlikon consumed that was supplied from grid electricity was 76.0%.
Our target of implementing energy management systems (EnMS) at all Oerlikon sites considers the installation of EnMS only at relevant sites (i.e. large operational and office sites), as it is neither economically nor sustainably prudent to have such systems implemented for small offices. The target included both ISO-50001-certified and Oerlikon defined EnMS.
The Oerlikon-defined EnMS is a stringent but lighter version of the energy management standards that closely mirror ISO 50001. The definitions of this system are documented in an internal guideline endorsed by management to regulate non-ISO sites. The local entities have the option to decide if they would implement the ISO 50001 or the Oerlikon-defined EnMS.
In 2022, 25 sites implemented EnMS, bringing the total number of Oerlikon sites with EnMS to 55, or 33% of our total relevant sites, and these sites account for 70.5% of Oerlikon’s total energy consumption. We have classified 23 of our sites as heavy energy users, consuming around 50% of our total global energy. All 23 sites were identified as priority sites and since first quarter of 2022, all of them have EnMS in place.
An EnMS allows us to address our energy impact, conserve resources and improve cost through efficient energy management. It is designed as a practical way for our sites to track, monitor and analyze their energy consumption so as to identify and implement improvement measures.
No. of Sites | % of Total Sites | |
EnMS according to: | ||
|
35 |
21% |
|
20 | 12% |
Total | 55 | 33% |
ISO 14001:2015 |
51 |
31% |
An EnMS provides a framework of requirements for each site to:
We engage in ongoing analysis to identify further successful practices that can be implemented across the Group and obstacles to reduce energy consumption that we need to manage more effectively. Our system for monitoring energy consumption at sites across the Group includes data collection on electricity usage on a monthly basis and other energies on a quarterly basis.
Oerlikon’s energy-consumption tracking system not only analyzes energy use, but also provides a breakdown of the proportion of electricity derived from renewable sources.
In 2022, 30% of our total electricity consumed was from renewable sources, representing an improvement of 8% points compared to our baseline of 22% in 2021. In terms of consumption, we increased the purchase of renewable energy by 41% from 68.8 GWh to 97.2 GWh, attributable to the additional 5 sites that have converted to renewable energy and improved data process and quality. To date, a total of 18 sites worldwide are using energy solely from renewable sources for electricity.
At many sites, our local teams are active in implementing energy-saving measures. For example, at a site in Suzhou, China, colleagues were encouraged to turn off lamps upon leaving the equipment room, which led to savings of around CHF 2 200 per year. At an Oerlikon Neumag site in Neumuenster, Germany, where carpet yarn machinery is produced, a new switch-off button was installed on the test run computer, making it easier to switch off the system when not in use, resulting in energy savings of 39%.
These individual examples (see also case studies and examples) may seem to deliver minor benefits. Collectively, they will make an impact in contributing to energy savings. In 2022, such initiatives resulted in 3.0 GWh of energy savings.
We are on track with our goals and remain committed to achieving our 2030 targets to have 100% of our relevant sites with EnMS implemented and to derive electrical energy solely from renewable sources.
Energy consumption within the organization1 | Unit |
20222 Total |
20213 Total |
2019 Total |
---|---|---|---|---|
Electrical power | GWh | 325.9 | 309.7 | 313.2 |
|
GWh | 97.2 | 68.8 | n.a. |
Natural gas | GWh | 60.8 | 64.8 | 38.9 |
Heat and cooling purchased | GWh | 14.2 | 14.8 | 25.9 |
Gasoline and diesel | GWh | 23.0 | 21.2 | 24.0 |
Other energies | GWh | 4.8 | 8.6 | 6.6 |
Total energy consumption | GWh | 428.8 | 419.0 | 408.6 |
1 Differences in total reported figure due to rounding.
2 Including 2021 acquisitions.
3 Excluding 2021 acquisitions.
Sandblasting is an important step in surface treatment for many applications. It removes dirt or roughens the surface so that the coating that is subsequently applied has better adhesion. At Oerlikon Metco in Chengdu, China, sandblasting machines and air compressors with two units are used.
If four or more sandblasting machines were working at the same time, one set of air compressors could not provide the necessary air pressure and two air compressors had to be opened at the same time. This led to a high and uneconomical consumption of electrical energy.
Adding an 80-liter air reservoir at the end of the compressed air conveying line solved the problem of insufficient pressure of the end units. As a result, two compressors no longer have to be opened simultaneously to generate the necessary pressure, saving over 120 MWh of electricity per year, or the annual energy consumption of around 30 private homes.
Oerlikon Barmag filament winders are produced in Remscheid, Germany. One of the most energy consuming but frequent operations in assembly is the shrinking of the chuck bushing. The heating up, joining and subsequent cooling creates a permanent force-fit connection of bushing and shaft.
With the optimization of the heating device by changing from radiant to inductive heating, the energy consumption was significantly reduced: on the one hand, due to higher energy efficiency of the device, on the other by reducing the heating zone by half. This resulted in energy savings of around 45 000 kWh/year and cost savings of more than EUR 10 000 per year.