Thanks to a structured vertical integration strategy, major processing is carried out in-house, ensuring a superior quality product that meets the high standards required by the luxury market.
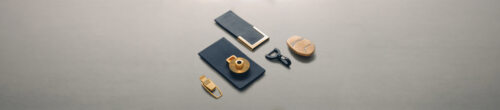
Thanks to a structured vertical integration strategy, major processing is carried out in-house, ensuring a superior quality product that meets the high standards required by the luxury market.
This technique allows us to easily handle not only quick sample and prototype requests but also direct production of medium/large runs. The advantage lies in the versatility, due to the absence of moulds, the level of detail, homogeneity and reproducibility of the pieces.
This stage is key to being able to achieve the level of customization that the customer expects from our accessories. Through this structured process, the final product is guaranteed to be manufactured efficiently, meeting the required specifications.
Through a plastic deformation process, brass parts are heated, compressed, shaped and cut. The hot-stamped items exhibit high hardness and tensile strength, tightness and precision tolerances.
Cold stamping involves plastic deformation of materials at room temperature or slightly heated. We are able to carry it out on both brass and steel. This process ensures high production speed, great resistance of the items and better yield during the surface treatment phase; it also reduces the possibility of defects on the component compared to other techniques.
Oerlikon Fineparts boasts a plant in Trento highly specialized in Metal Injection Moulding. MIM combines polymer injection moulding technologies with powder metallurgy: a mixture of metal powders and an appropriate polymer are injected into a mould in order to create an object of defined geometry. The moulded part follows a series of processes to remove the polymer and consolidate the powder to produce a metallic solid, characterized by high mechanical properties, structural complexity and excellent surface finish. Thanks to the know-how acquired, we are also able to manage the mould design phase in-house.
Polishing is essential to improve the surface finish of materials, making them more suitable for the next steps of processing. We can perform it either through a manual process, which involves greater precision and flexibility, or an automatic one, that allows for faster times and efficient treatment of large volumes.
Through this process, it is possible to obtain metal items that can be customized down to the smallest details; in fact, it allows for the high levels of precision and geometric complexity required by the luxury world. We are able to perform it on brass, bronze and silver.
The Palazzolo sull'Oglio plant carries out Zamak die casting operations for both the Oerlikon Fineparts and Oerlikon Riri brands. This method is particularly effective for producing lightweight, corrosion-resistant and easily processed precision components in-house.
Performing certain machining operations, including milling, turning and laser cutting, with Computerized Numerical Control machines has a number of advantages: precision, ability to produce significant quantities, flexibility, high automation and efficiency.
This process aims to refine the surface of metal components through the use of mechanical vibration, which causes friction between the parts and the abrasive material. In this way, external irregularities are removed, improving the finish appearance.
Electroforming is a manufacturing process that involves the electrodeposition of a layer of metal into a matrix capable of conducting electric current. This process is particularly used in the jewelry industry, where a complex level of detail and precision is required on items that need to be light.
At the Arezzo plant, where Oerlikon Fineparts' fashion jewels are designed and manufactured, the assembly phase of crystals, zircons and, in general, precious stones is carried out. This process embodies the precision manufacturing and craftsmanship typical of the Tuscan goldsmithing tradition.
The final assembly stage, which includes components preparation, assembly and last inspection, is also performed in-house, allowing us to further optimize the efficiency of the production process.